我國高純石墨生產工藝是怎么樣的?
高純石墨是指碳含量大于99.99%的石墨。高純石墨具有耐高溫、耐腐蝕、抗熱震、低熱膨脹系數、自潤滑、低阻力系數和易加工等優點。廣泛應用于冶金、機械、環保、化工、電子、醫藥、軍工、航空航天等領域,在國民經濟尤其是太陽能光伏產業中發揮著越來越重要的作用。全球太陽能光伏產業年均增長率為40%。作為世界上最大的太陽能光伏生產國,中國的份額達到世界總量的70%。2011年,該行業消耗了23,000多噸高級石墨材料。預計光伏行業單晶硅和多晶硅對高純石墨材料的需求每年將增長20% ~ 25%。
目前,我國石墨工業技術在世界上仍處于中低水平。產品多為原料和初級加工品,產品中的高雜質限制了其應用范圍。因此,一方面,國內石墨產品在國際市場上價格低廉,導致大量石墨資源外流;另一方面,國內市場需要的高純超細石墨制品大多依賴進口。綜上所述,開展高純石墨生產技術的研究,提高產品質量,對我國高純石墨產業的發展具有深遠的意義。
1.國內外高純石墨生產工藝的特點及比較2.1高純石墨生產工藝的特點
目前高純石墨生產工藝的主要流程如圖1所示,其流程為:煅燒/提純→捏合→壓制→焙燒→浸漬→石墨化。國內的生產流程是:煅燒/提純→捏合→壓制→第一次烘烤→第一次浸泡→第二次烘烤→第二次浸泡→第三次烘烤(→第三次浸泡→第四次烘烤→)石墨化。從技術上看,國內生產高純石墨是以石油焦或煤焦油瀝青為主要原料,通過提純的方式除去部分灰分、非金屬和金屬氧化物雜質,然后將除去雜質的原料用粘結劑按一定比例捏合而成。將得到的粉末顆粒通過冷等靜壓成型,反復焙燒和浸漬,最后將焙燒產物石墨化,得到高純石墨。
國外的生產工藝是:煅燒/提純→捏合→熱等靜壓→一次烘烤(→一次浸泡→二次烘烤→)石墨化。國外直接采用熱等靜壓(HIP),得到的壓坯致密性更好,更容易進行后續的焙燒和石墨化。坯體一次壓制焙燒即可達到石墨化的要求,節省大量時間,提高工作效率。
1.1高純石墨生產工藝的比較
雖然國內外高純石墨的生產技術大致相似,但仍有一些差異。對比如下:(1)中國的制作工藝復雜,需要反復烤、浸才能達到制作目的。這導致較高的生產成本和較低的產量。
(2)提純方法有多種,如浮選法、堿酸法、氫氟酸法、氯化焙燒法、高溫法等。浮選法是利用石墨的可浮性來富集和提純石墨。浮選后,石墨原礦的最終精礦品位通常為90%左右。酸法提純石墨的原理是石墨中的硅酸鹽、應時等雜質與氫氧化鈉反應,然后水洗脫硅。例如,一些金屬氧化物雜質用酸浸出,然后通過過濾和洗滌與石墨分離。酸法可獲得固定碳含量大于99%的石墨產品。氫氟酸法是利用石墨中的雜質與氫氟酸反應生成氟化物和易溶于水的揮發物,達到提純的目的。日本、法國等國專利介紹,用氟化氫銨或氟化銨與含碳量為93%的石墨粉反應,可將石墨的固定碳含量提高到99.95%。
焙燒法是將石墨粉與一定量的還原劑混合,在一定溫度和特定氣氛下焙燒,然后通入氯氣進行化學反應,使物料中的有價金屬轉化為氣態或凝聚相的氯化物和低熔點的絡合物而逸出,從而與其他組分分離,達到提純石墨的目的。一般來說,石墨的純度可以大于98%。
采用高溫法是因為石墨是自然界中熔點最高的物質之一,熔點為(3850±50)℃,沸點為4 500℃,而硅酸鹽礦物的沸點均低于2 750℃(應時沸點)。石墨的沸點比雜質硅酸鹽的沸點高得多,因此可以除去雜質。一般情況下,通過高溫加熱到2 700℃以上,石墨制品的含碳量可以達到99.99%以上。對于以上方法,每種方法都有各自的優缺點。國內外企業根據自身原料的特性和純度要求,選擇合適的提純方法。
(3)不同的成型工藝。目前,國內各大高純石墨生產企業主要采用冷等靜壓工藝。熱等靜壓具有石墨粉致密、生坯密度分布均勻、各向異性系數小的優點。國外采用的是熱等靜壓,這是一種使材料在高溫高壓的同時作用下進行等靜壓的工藝技術。不僅提高了壓坯的致密性,而且節省了時間,提高了工作效率。
(4)石墨化過程不同。目前國內大部分企業使用的石墨化設備是Acheson石墨化爐,而國外多采用內熱式縱向石墨化爐。
2生產高純石墨的一般過程
高純石墨的主要生產過程如圖1所示。顯然,高純石墨的生產工藝不同于石墨電極的生產工藝。高純石墨需要結構上各向同性的原料,需要磨成更細的粉末,需要應用等靜壓技術,所以烘烤周期長。為了達到理想的密度,需要多次浸漬-烘烤循環,石墨化周期比普通石墨長得多。
2.1原材料
生產高純石墨的原料包括骨料、粘結劑和浸漬劑。集料通常是針狀石油焦和瀝青焦。這是因為針狀石油焦具有灰分低(一般小于1%)、高溫下易石墨化、導電導熱性能好、線膨脹系數低的特點。在相同的石墨化溫度下由瀝青焦獲得的石墨具有更高的電阻率,但是具有更高的機械強度。所以一般來說,除了石油焦之外還會使用一定比例的瀝青焦來提高產品的機械強度。煤焦油瀝青通常用作粘結劑,它是煤焦油蒸餾的產物。室溫下為黑色固體,無固定熔點。根據各企業不同的設備條件和工藝要求,使用的煤瀝青軟化點在50℃-250℃之間。一般用中溫或高溫煤焦油瀝青生產高純石墨產品。浸漬劑與粘合劑基本相同。它是提高產品的堆積密度、抗滲性、潤滑性、強度等特殊性能。烘烤或石墨化加工后需要加入浸漬劑。
2.2煅燒/提純
由于其不同的成焦溫度或成煤地質年齡,所選聚集體的內部結構中不同程度地含有水分、雜質或揮發物。如果不事先排除這些物質,直接用于生產石墨材料,必然影響產品質量和使用性能。因此,應煅燒或提純所選骨料。煅燒是在隔絕空氣的條件下,對各種固體碳原料進行的高溫熱處理。在低溫干燥階段,主要是去除水分;在揮發份排出階段,主要完成原料中芳香族化合物的分解和部分化合物的縮聚。提純主要是去除一些雜質。目前,國內外提純石墨的方法主要有浮選法、堿酸法、氫氟酸法、氯化焙燒法、高溫法等。
2.3研磨
石墨生產中使用的固體物料,雖然煅燒或提純后的物料塊度有所減小,但粒度仍然較大,波動較大,成分不均勻,所以需要將骨料粒度破碎到配料的要求。高純石墨的聚集尺寸通常達到20μm..目前,立式輥磨機用于研磨平均粒度為10 ~ 20μ m的粉末
2.4揉捏
研磨后的粉末分散且不均勻。需要與煤焦油瀝青粘結劑按一定比例混合后放入加熱的捏合機中捏合,使物料分布均勻,粘結劑薄而均勻地包裹在粉體顆粒表面,滲入粉體顆粒表面的微孔中。
2.5成型
目前炭素生產的成型方法很多,主要有四種:擠壓成型(圖2a)、壓縮成型(圖2b)、振動成型和等靜壓成型(圖2c)。高純石墨的生產采用等靜壓,包括冷等靜壓和熱等靜壓。等靜壓成型是指將材料放入軟模具中,壓實密封,抽真空,放入等靜壓機的氣缸中。模具外的液體以相同的壓力從各個方向作用在模具上,被壓成圓柱形或長方形的制品】。得到的產品結構和性能各向同性,這是等靜壓產品的最大優勢。
2.6烘烤
成型后的炭素制品要經過焙燒,即在隔絕空氣的條件下對壓制的生坯進行熱處理(約1 000℃),使粘結劑碳化成粘結劑焦。這是一個緩慢的過程。整個過程分為幾個階段,每個階段都進行一系列的物理化學反應,包括在碳集料表面形成一定厚度的粘結劑焦膜、粘結劑的液相遷移、瀝青蒸氣的毛細凝結、氣化和表面擴散等。
2.7浸漬
浸漬的目的是用熔融瀝青等浸漬劑填充焙燒過程中在制品中形成的微小孔隙和集料焦炭顆粒中原有的開孔,以提高制品的堆積密度、導電性、機械強度和耐化學腐蝕性。通常,浸漬是通過壓力浸漬法進行的。產品應先預熱,然后在浸漬罐中真空脫氣,再將熔融的煤焦油瀝青加入浸漬罐中,浸漬劑瀝青加壓進入產品。
2.8石墨化
石墨化是指通過熱活化將熱不穩定的非石墨碳轉化為石墨碳的高溫熱處理過程。經過2000 ~ 2800℃的石墨化處理后,無序層狀結構的炭素制品的碳原子晶格轉變為三維有序層狀結構,同時去除了雜質。石墨化方法有艾奇遜法、內熱串聯法、中頻感應法等。
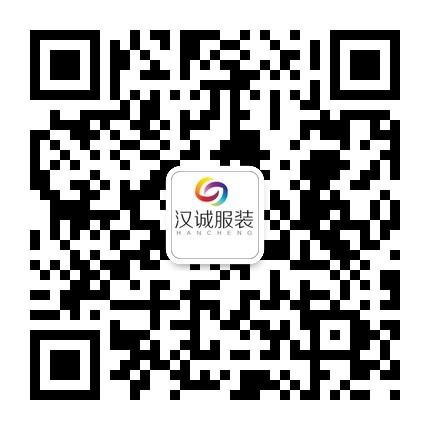
