介紹石墨電極生產加工工藝流程
石墨電極生產加工工藝流程如下:
1)石墨浸油。石墨材料在機械加工之前,應該在機油內浸數十小時,使油滲入石墨材料,以使機械加工時灰粉不致飛揚,并能得到較光滑的表面。
2)涂漆劃線。電極在外形表面粗加工以后,在劃線表面噴涂一層很薄的白漆再進行劃線,這樣線條清晰,便于機械加工。
3)進行機械加工。
石墨電極的質量指標:
反映石墨電極質量和使用性能的指標主要有:體積密度dp、電阻率ρ、抗折強度σ、彈性模量E熱膨脹系數a和灰分A% .根據這幾項指標的差異以及原料和制造工藝的不同,國家標準(YB/T 4088/89/90-2000)中將石墨電極分為普通功率石墨電極(RP)、高功率石墨電極(HP)、超高功率石墨電極UHP)三種。后石墨電極生產廠根據用戶使用需求增加了高體密石墨電極(HD)和準超高石墨電極(SHP )兩種。
石墨電極的消耗機理:
石墨電極在電爐煉鋼中的消耗量主要與電極本身質量有關,也與煉鋼的爐況(如爐子新舊、有無機械故障、是否連續生產等)和煉鋼操作(如冶煉鋼種、吹氧時間、爐料情況等)關系很大。這里只探討石墨電極本身的消耗情況,其消耗機理有以下幾方面:端部消耗包括 電弧高溫引起的石墨材料升華以及電極端部與鋼水及爐渣發生化學反應的損失。端部高溫升華速率主要取決于通過電極的電流密度,其次與電極側部氧化后的直徑大小有關,端部消耗還與是否用電極插入鋼水增炭有關。
側部氧化電極的化學 成分是碳,碳在定條件下與空氣、水蒸氣、二氧化碳都會發生氧化反應,電極側部氧化量與單位氧化速率和暴露面積有關。般 情況下,電極側部氧化量要占電極總消耗量的50%左右.近年來為了提高電爐冶煉速度,更增加了吹氧操作的頻次,導致電極的氧化損失增加。在煉鋼過程中經常觀察電極軀干的發紅程度和下端的錐度是衡量電極抗氧化能力的直觀方法。
殘端損失電極連續使用到上下兩根電極連接處時,小段電極或接頭(即殘體)因本體的氧化變細或裂紋的貫通而產生脫離。殘端損失的大小與接頭形狀扣型、電極內部結構、電極柱的振動、撞擊有關。
表面剝落及掉塊在冶煉過程中 急冷急熱,電極自身的抗熱振 性能差導致的結果。電極折斷包括電極軀 干折斷和接頭折斷。電極折斷與石墨電極和接頭的自身質量、加工配合有關,也與煉鋼操作有關,產生原因往往是鋼廠與電極生產廠爭議的焦點。
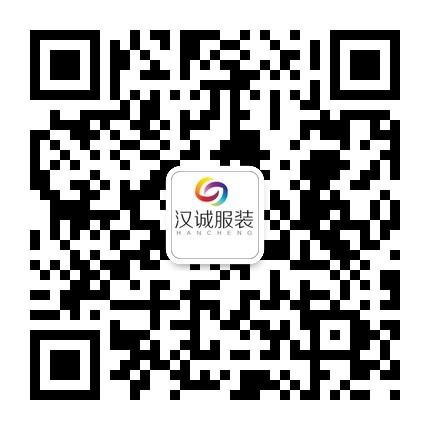
