換熱器管管板角焊縫焊接質量的控制
越來越多的用戶對換熱器管 管板角焊縫的焊接質量提出了更高的要求。
滲透方法僅能檢測表面開口缺陷,不能發現內部缺陷,對控制其內在質量效果不好。射線檢測要求特殊形狀的膠片和對應不同管徑的厚度補償,透照焦距難以把握,不便于放置像質計等。這時檢測工藝可在供需雙方協商一致的前提下加以使用。但是要加以推廣普及,難免會在經濟性和實用性上遇到阻礙。在此介紹一種易于實現和普及的管 管板角焊縫內在焊接質量控制方法。此法在筆者所在公司承制的換熱器產品上得以應用,可滿足要求。
1、管板焊接試樣的制作管
管板焊接試樣的制作要求完全與產品上管 管板焊縫相同。試板管孔的布局采用正方形排列(圖1),試板厚度b1≮20mm,管孔中心距、坡口形式及管與管板的裝配形式按標準或設計圖樣的要求,焊接方法為手工氬弧焊打底及蓋面,焊接過程中應記錄焊接工藝參數(如氬氣流量、焊接電壓、焊接速度、焊接電流與極性、焊絲牌號及直徑、添絲與否及速度、是否加脈沖及脈沖參數、焊槍角度以及選用設備的型號等),以改進焊接質量。管 管板試樣焊制后,沿管板厚度進行線切割或從焊縫側的對面進行精加工,使試樣最終厚度為7~10mm。
2、焊接試樣的無損檢測
先對試樣進行滲透檢測,以保證其表面質量,再進行射線檢測。透照時,應先劃分好透照區域,作好標。如換熱管參數為19mm×2mm,按圖1所示試樣用兩張180mm×80mm規格的膠片即可,其它規格的換熱管可根據實際情況而定。透照時,將有焊縫的一側緊貼膠片,膠片背面放置一塊防護用鉛板或廢增感屏,以防止散射線,提高清晰度。朝上的側面上放置相應的像質計和標記等。選用合適的曝光條件進行透照,底片黑度達到2.5左右為最佳。
底片上可清晰觀察到管 管板焊縫中的各種缺陷(如氣孔、夾鎢、未熔合或未焊透等,見圖2中1~3)。解剖試板時可根據底片上缺陷部位確定切割方向,解剖后可清晰觀察并區分未熔合和未焊透。
試板焊縫表面及反面與焊縫對應的部位可預先制作人工缺陷(如鉆孔),人工缺陷的最大尺寸(鉆孔的直徑和深度)為焊縫中允許存在的缺陷最大尺寸。在射線照相底片上能清晰反映出人工缺陷的形狀和位置。此法證明將試樣厚度加工到7~10mm時,保證有足夠的檢測靈敏度。
3、焊接工藝的改進與質量控制
當試件焊縫中存在各種缺陷,根據相關標準[4]或客戶的要求評定為不合格時,需要改進焊接工藝,然后重新進行試樣的制作,并將參數的變化記錄在案,以利前后比較。重復上述步驟,直到焊縫焊接質量滿足要求為止。這樣可以針對焊接參數變化與焊接質量的變化進行分析,查找影響焊接質量的主次要原因,采取相應措施分別進行糾正和預防。
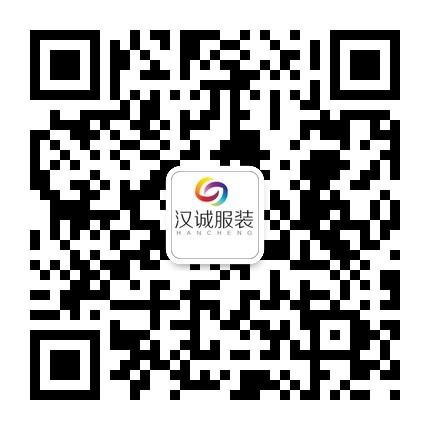
