講述膨脹石墨的制備方法
1、電化學氧化法
將定量鱗片石墨裝置成陽極,用不銹鋼或鉑作陽極集流器,浸在一定濃度的H2SO4水溶液中,用鉛板或鉑板作陰極,用恒定電流進行電解,后續處理得膨脹石墨。此外,可以改用硝酸銨等可分解鹽作插層劑代替H2SO4水溶液。通電使陽極氧化,電解液分解出硝酸根離子作插層物質。使整個生產過程沒有強酸、強堿、強氧化劑的介入,不僅極大地降低了生產成本、延長設備的使用壽命,而且還減少污染,使產品不含硫而質量大為提高,其可操作性也明顯增強。
于仁光等以有機-無機混酸溶液為介質用電化學法制備了膨脹石墨,并用掃描電子顯微鏡(SEM)觀察其表面形貌,膨脹后的石墨具有豐富的網絡狀結構,形成吸附油的儲存空間。膨脹石墨對重油的吸附量隨著膨脹容積的增大而增加,合適的電流密度、電解液濃度以及反應時間是制備高膨脹容積膨脹石墨的關鍵。
甘偉兵等以晶質鱗片石墨為原料,采用電化學陽極氧化法生產膨脹石墨。系統地探討了酸液濃度、電流密度、氧化時間等因素對硫酸石墨鹽生成量及膨脹率的影響,獲得了最佳工藝參數,酸液濃度18mol/l,電流密度42mA/cm2,氧化時間20min,生產出膨脹率達300多倍的膨脹石墨。
2、化學氧化法
化學氧化法就是將氧化劑、插層劑與鱗片石墨混合后,在一定溫度下充分反應再進行水洗和干燥。制備過程中,氧化劑和插層劑的種類、濃度以及反應的溫度、時間等都是影響膨脹石墨性能的重要因素。化學氧化法是工業上應用最多和最成熟的方法。
目前化學氧化法制備可膨脹石墨主要是采用濃硫酸為主體來制備可膨脹石墨,配以各種氧化劑,與天然鱗片石墨反應而成。但該法制備的膨脹石墨,硫的質量分數高達 2.8%-4.5%,用作密封材料時,殘存的硫會促進石墨-金屬間的電化學反應,造成金屬的腐蝕,并且抗氧化能力較差,在環境溫度較高,且有氧化劑存在的條件下,極易被氧化,使密封效果下降,嚴重的會導致密封失效,發生工業事故。這一問題已成為可膨脹石墨制品推廣應用的嚴重障礙。目前制備無硫膨脹石墨成為研究熱點。
萬為敏等采用化學方法制備了無硫可膨脹石墨,并對其最佳工藝條件進行了探討。以高錳酸鉀為氧化劑,以硝酸和磷酸為插入劑,以天然鱗片石墨為基質制備了無硫可膨脹石墨。制備的適宜條件為石墨(g)∶混酸(ml)∶高錳酸鉀(g)=1.0∶10∶0.2,反應溫度45℃,反應時間為80min。所得到的無硫可膨脹石墨經水洗至pH值為5-7,烘干后在900℃-1000℃的高溫下膨脹,即得無硫膨脹石墨。與已有方法相比,用此法制備的膨脹石墨不含硫,膨脹倍率高,膨脹充分。盛曉穎等以硝酸和雙氧水為氧化劑,乙酸為插層劑,采用化學氧化法制備了無硫可膨脹石墨,得出在石墨取5g,氧化時間為60min,反應溫度為25℃條件下,硝酸、雙氧水、乙酸的體積比為12∶1∶5時,得到最大膨脹體積為310mL/g。該膨脹石墨具有密封性、耐腐蝕、膨脹體積大的優點。
3、氣相擴散法
氣相擴散法是將石墨和插層物分別置于真空密封管的兩端,在插層物端加熱,利用兩端的溫差形成必要反應壓差,使得插層物以小分子的狀態進入鱗片石墨層間,從而制得石墨層間化合物。此種方法生產的產品階層數可控制,但其生產成本高。
4、爆炸法
爆炸法制備膨脹石墨,通常采用KClO4、Zn(NO3)2·2H2O、HClO4等作為膨脹劑與石墨制成混合物或煙火藥,加熱或引燃后,利用煙火藥低速爆炸時產生的熱量,同時產生氧化相和插層物,從而使石墨發生“爆炸”式的膨化,制得膨脹石墨。
5、微波法
采用傳統高溫膨化法制備的膨脹石墨,升至高溫需要一定的時間,且膨脹過程中電能的消耗較大。通過采用微波對石墨進行膨化處理,操作方便過程易控,具有高效和節能的優點。
采用微波法,對石墨進行膨化處理,通過控制微波加熱的功率、時間等參數,可容易地調整對石墨的處理。結果表明:達到最優膨脹過程時大鱗片石墨的微波膨脹時間比細鱗片石墨的長,同時在輸出功率上大鱗片石墨也比細鱗片石墨的大;與傳統的高溫膨化法相比,微波法開停方便,具有高效和節能的優點,更適合細鱗片石墨的膨脹。
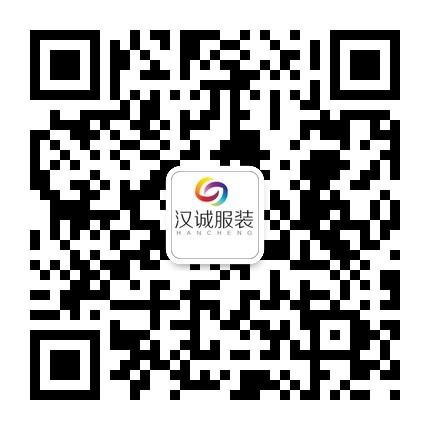
